Unlocking Precision: The Evolution of CNC Machining Machines
2024-11-19
Unlocking Precision: The Evolution of CNC Machining Machines
Table of Contents
- 1. Introduction to CNC Machining
- 2. A Brief History of CNC Machining Machines
- 3. How CNC Machining Works
- 4. Advantages of CNC Machining
- 5. Applications of CNC Machining in Various Industries
- 6. Technological Advancements in CNC Machining
- 7. Future Trends in CNC Machining
- 8. Frequently Asked Questions (FAQs)
- 9. Conclusion
1. Introduction to CNC Machining
CNC (Computer Numerical Control) machining has revolutionized the manufacturing industry, transforming traditional machining processes into highly automated and precise methods. By utilizing computer systems to control machines, CNC machining enhances the accuracy and efficiency of producing intricate components in a variety of materials. The automation of machining processes through CNC technology not only improves productivity but also ensures consistency and quality in manufacturing.
2. A Brief History of CNC Machining Machines
The evolution of CNC machining machines can be traced back to the 1940s when the first numerical control machines were developed. Initially, these machines relied on punched tape technology to execute commands, which marked a significant departure from manual machining. Over the decades, with advancements in computer technology, CNC machines became more sophisticated, leading to the development of modern CNC machining centers that offer unparalleled precision and user-friendliness.
2.1 The Birth of Numerical Control
In the late 1940s, engineers began experimenting with mechanical devices that could follow numerical instructions. The first successful implementation of numerical control (NC) machines was seen in the 1950s, allowing for more efficient and complex machining tasks.
2.2 Transition to Computer Numerical Control
By the 1960s, the introduction of computers to control machining processes led to the birth of CNC machines. This transition allowed for greater flexibility, as programs could be modified and stored digitally, paving the way for the modern CNC systems we see today.
3. How CNC Machining Works
CNC machining operates through a precise sequence of steps that convert a digital design into a physical component. The process begins with CAD (Computer-Aided Design) software, where engineers create detailed designs of the parts to be manufactured. These designs are then translated into G-code, a language that CNC machines understand.
3.1 The Role of CAD/CAM Software
CAD/CAM (Computer-Aided Design/Computer-Aided Manufacturing) software plays a crucial role in CNC machining. It allows engineers to visualize their designs and simulate machining processes before actual production begins, minimizing errors and optimizing efficiency.
3.2 Machine Operation and Tooling
Once the G-code is generated, it is uploaded to the CNC machine, which interprets the instructions to control the movement of tools along various axes (X, Y, Z). The machine then precisely cuts, mills, or drills the material, following the designated paths to create the desired shape.
4. Advantages of CNC Machining
CNC machining offers numerous advantages over traditional machining methods, making it a preferred choice for manufacturers around the globe.
4.1 Increased Precision and Accuracy
One of the key benefits of CNC machining is its ability to produce highly precise parts. The computer-controlled process minimizes human error, ensuring that each component meets exact specifications.
4.2 Enhanced Efficiency and Speed
CNC machines can operate continuously without fatigue, significantly increasing production rates. Complex parts can be manufactured in a fraction of the time it would take using manual methods.
4.3 Flexibility in Design
CNC machining allows for quick adjustments to designs, making it easy to modify existing products or create prototypes. This flexibility is invaluable in industries that require rapid innovation.
4.4 Improved Safety
With automated processes, the risk of accidents and injuries in the workplace is reduced. Operators can set up machines remotely and monitor their progress from a safe distance.
5. Applications of CNC Machining in Various Industries
CNC machining is employed across numerous sectors, highlighting its versatility and importance in modern manufacturing.
5.1 Aerospace and Defense
The aerospace industry relies heavily on CNC machining for producing components that demand the highest levels of precision, such as aircraft frames and turbine parts.
5.2 Automotive
In the automotive sector, CNC machining is used to manufacture everything from engine components to custom parts, ensuring quality and durability.
5.3 Medical Devices
CNC machining plays a critical role in the production of medical devices, where precision is essential for functionality and patient safety.
5.4 Electronics
The electronics industry utilizes CNC machining for creating intricate circuit boards and components, ensuring that they meet strict performance standards.
6. Technological Advancements in CNC Machining
As technology continues to advance, CNC machining is also evolving. Recent innovations enhance functionality, increase precision, and improve efficiency.
6.1 Integration of IoT and AI
The integration of Internet of Things (IoT) and Artificial Intelligence (AI) in CNC machining allows for real-time monitoring and predictive maintenance, optimizing machine performance and reducing downtime.
6.2 3D Printing and CNC Hybrid Systems
The development of hybrid systems that combine CNC machining with 3D printing capabilities expands the possibilities for creating complex geometries and customized parts.
6.3 Enhanced Materials and Tooling
Innovations in materials and tooling have led to the development of stronger, more durable components that enhance the performance of CNC machines and the quality of the finished products.
7. Future Trends in CNC Machining
Looking ahead, several trends are poised to shape the future of CNC machining.
7.1 Automation and Robotics
The increasing automation of CNC machining processes through robotics will further streamline production, reduce labor costs, and enhance operational efficiency.
7.2 Sustainability Practices
As industries focus on sustainability, CNC machining will likely evolve to incorporate eco-friendly materials and practices that minimize waste and energy consumption.
7.3 Customization and On-Demand Manufacturing
The demand for customized products is on the rise, and CNC machining is well-suited to meet this need through rapid prototyping and flexible manufacturing capabilities.
8. Frequently Asked Questions (FAQs)
8.1 What is CNC machining?
CNC machining is a manufacturing process that uses computer-controlled machines to create precise parts and components from various materials.
8.2 How does CNC machining improve manufacturing efficiency?
CNC machining enhances manufacturing efficiency by automating processes, allowing for faster production rates, and minimizing human error.
8.3 What industries commonly use CNC machining?
CNC machining is widely used in industries such as aerospace, automotive, medical devices, electronics, and many more.
8.4 Can CNC machines handle complex designs?
Yes, CNC machines excel at producing complex designs due to their precise control and the ability to follow intricate G-code instructions.
8.5 What are the future trends in CNC machining technology?
Future trends include increased automation, integration of IoT and AI, sustainable practices, and an emphasis on customization and on-demand manufacturing.
9. Conclusion
CNC machining has come a long way since its inception, evolving into a vital component of modern manufacturing. Its ability to deliver unparalleled precision, efficiency, and flexibility has made it indispensable across various industries. As we look to the future, ongoing technological advancements promise to further enhance CNC machining capabilities, ensuring that it remains at the forefront of manufacturing innovation. Embracing these developments will undoubtedly unlock new levels of precision and efficiency, maintaining CNC machining's crucial role in shaping the future of production.
Recommend News
National Service Hotline
Guangzhou Feihong Intelligent Technology Co., Ltd.
Telephone 86 20 66606238 / 86 20 86920099 / 86 20 86920418 / 86 20 86920578
Fax: 86 20 86920126
Address: No. 118, Middle Section of Furong Avenue, Huadu District, Guangzhou City, Guangdong Province, China
Zip Code: 510860
E-mail:feihong@feihong-machine.com
Website:www.feihong-machine.com
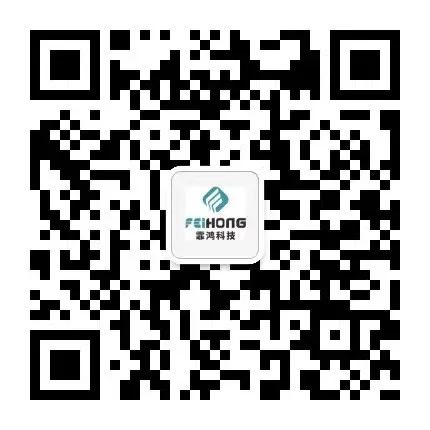

Follow us
© 2022 Guangzhou Feihong Intelligent Technology Co., Ltd. SEO Tags Powered by www.300.cn City Product
Business License
WhatsApp: 15013026621
Add:fu Rong Road,Huadu District, Guangzhou City, China.
Email: feihong@feihong-machine.com
We will provide you with timely feedback