Five-Axis Machining Centers: Revolutionizing the Manufacturing Process
2025-07-13
Five-Axis Machining Centers: Revolutionizing the Manufacturing Process
Understanding the Technology Behind Five-Axis Machining
Five-axis machining centers represent a significant advancement in manufacturing technology. Unlike traditional three-axis machines, which can only move along the X, Y, and Z axes, five-axis machines offer two additional rotational axes. This capability allows for the machining of complex geometries and intricate designs without the need for repositioning the workpiece, significantly reducing production time and enhancing accuracy.
The Basics of Five-Axis Machining
Five-axis machining involves simultaneous movement along all five axes, which provides manufacturers with several advantages:
- **Enhanced Accuracy:** The ability to machine parts in a single setup minimizes the chance of errors typically associated with multiple setups.
- **Complex Geometries:** The versatility of five-axis machining allows for the creation of intricate shapes and features that are impossible or impractical to achieve with three-axis machines.
- **Improved Tool Life:** By positioning tools in optimal angles, five-axis machining reduces tool wear, resulting in longer tool life.
Types of Five-Axis Machining Centers
There are two main types of five-axis machining centers: articulated and trunnion-style.
- **Articulated Machines:** These machines utilize a rotating arm that can move around multiple axes, mimicking a human arm's movement. Articulated five-axis machines are ideal for complex shapes and intricate detailing.
- **Trunnion-Style Machines:** These machines have a rotating table that allows the workpiece to be tilted and rotated easily. Trunnion-style machines are suitable for larger workpieces and often offer higher rigidity.
The Benefits of Five-Axis Machining Centers
Investing in five-axis machining centers can yield significant benefits for manufacturers across various industries.
Increased Efficiency and Productivity
By reducing the number of setups required to complete a part, five-axis machines streamline the manufacturing process. This efficiency translates into higher productivity levels, allowing manufacturers to meet tight deadlines and increase output without compromising quality.
Cost-Effectiveness
While the initial investment in five-axis machining centers can be significant, the long-term cost savings are notable. Reduced labor costs, lower scrap rates, and efficient use of materials contribute to a more cost-effective manufacturing process.
Superior Quality and Precision
Five-axis machining centers are designed to achieve tighter tolerances and superior surface finishes. This precision is vital for industries such as aerospace, automotive, and medical, where quality cannot be compromised.
Flexibility in Design and Manufacturing
With the ability to machine complex geometries, manufacturers can easily adapt to changing design requirements. This flexibility is crucial in today's fast-paced market, where innovation and customization are key to staying competitive.
Applications of Five-Axis Machining Centers
The applications for five-axis machining centers are vast and varied, impacting numerous industries.
Aerospace Industry
In the aerospace sector, five-axis machining is essential for fabricating components like turbine blades and airframe parts. The ability to achieve lightweight designs with high strength-to-weight ratios is critical for aircraft efficiency.
Medical Device Manufacturing
The medical industry relies on five-axis machining for producing components that require high precision, such as surgical instruments and implants. The ability to create intricate designs with tight tolerances is vital for ensuring patient safety and the effectiveness of medical devices.
Automotive Manufacturing
Automotive manufacturers utilize five-axis machining for a variety of components, including engine blocks, transmission housings, and custom parts. The technology allows for lightweight designs that contribute to improved fuel efficiency and performance.
Tooling and Die Making
Five-axis machining is widely used in tooling and die-making processes. The ability to create complex shapes and features in a single setup reduces production time and enhances the overall quality of the tooling.
Choosing the Right Five-Axis Machining Center
Selecting the right five-axis machining center involves several considerations.
Assessing Your Manufacturing Needs
Before investing in a five-axis machining center, evaluate your specific manufacturing needs. Consider factors such as:
- **Part Size and Complexity:** Determine the types of parts you will be machining and their required geometries.
- **Material Types:** Different materials may require different machining strategies, so understanding your material requirements is essential.
- **Production Volume:** Assess your production volume to choose a machine that meets your output requirements without underutilization.
Evaluating Machine Specifications
When comparing five-axis machines, pay close attention to:
- **Axis Configuration:** Understand the type of five-axis configuration that best suits your applications, whether articulated or trunnion-style.
- **Spindle Speed and Power:** Higher spindle speeds and power ratings can improve machining performance and efficiency.
- **Control Software:** Advanced control software can enhance the machine's capabilities, making it easier to program complex parts.
Maintenance and Longevity of Five-Axis Machining Centers
Proper maintenance is crucial for ensuring the longevity and optimal performance of five-axis machining centers.
Routine Maintenance Practices
Implement routine maintenance practices to prevent issues and maximize machine uptime:
- **Regular Cleaning:** Keep the machine clean to prevent dust and debris from affecting performance.
- **Lubrication:** Regularly check and replenish lubrication levels to ensure smooth operation.
- **Calibration:** Periodic calibration of the machine can help maintain accuracy and precision.
Signs of Wear and How to Address Them
Be vigilant for signs of wear, such as unusual noises, decreased performance, or inaccurate machining. Addressing these issues promptly can prevent costly repairs and downtime.
Future Trends in Five-Axis Machining Technology
The future of five-axis machining centers is bright, with several trends shaping the industry.
Integration of Automation and Robotics
The integration of automation and robotics into five-axis machining operations is on the rise. Automation streamlines processes, reduces labor costs, and improves efficiency.
Advancements in CAD/CAM Software
As CAD/CAM software continues to evolve, it will enable manufacturers to design more complex parts with ease. Enhanced software capabilities will streamline programming and improve overall machining efficiency.
Increased Focus on Sustainability
Sustainability is becoming increasingly important in manufacturing. Five-axis machining centers can contribute to greener processes by reducing waste, improving material utilization, and lowering energy consumption.
FAQs About Five-Axis Machining Centers
1. What is the primary advantage of using a five-axis machining center?
The primary advantage is the ability to machine complex parts in a single setup, which reduces production time and improves accuracy.
2. How does five-axis machining compare to traditional machining?
Five-axis machining offers greater versatility, precision, and efficiency compared to traditional three-axis machining, making it suitable for more intricate designs.
3. What industries benefit the most from five-axis machining technology?
Industries such as aerospace, automotive, medical device manufacturing, and tooling all benefit significantly from five-axis machining technology.
4. Are five-axis machining centers suitable for small production runs?
Yes, five-axis machining centers are ideal for small production runs, as they allow for quick changes in designs and can efficiently produce complex parts.
5. What should I consider when selecting a five-axis machining center?
Consider factors such as part size, material types, production volume, axis configuration, spindle speed, and the control software when selecting a machine.
Conclusion
Five-axis machining centers are revolutionizing the manufacturing process by providing unparalleled precision, efficiency, and versatility. With their ability to produce complex geometries with reduced setup times, these machines are essential for modern manufacturing across various industries. As technology continues to advance, embracing five-axis machining will enable manufacturers to stay competitive and meet the evolving demands of the market. Investing in this technology is not just a choice; it's a strategic move towards future-proofing manufacturing operations.
Recommend News
National Service Hotline
Guangzhou Feihong Intelligent Technology Co., Ltd.
Telephone 86 20 66606238 / 86 20 86920099 / 86 20 86920418 / 86 20 86920578
Fax: 86 20 86920126
Address: No. 118, Middle Section of Furong Avenue, Huadu District, Guangzhou City, Guangdong Province, China
Zip Code: 510860
E-mail:feihong@feihong-machine.com
Website:www.feihong-machine.com
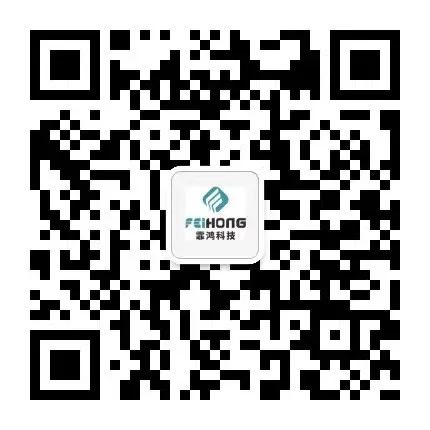

Follow us
© 2022 Guangzhou Feihong Intelligent Technology Co., Ltd. SEO Tags Powered by www.300.cn City Product
Business License
WhatsApp: 15013026621
Add:fu Rong Road,Huadu District, Guangzhou City, China.
Email: feihong@feihong-machine.com
We will provide you with timely feedback